SERVICES
Rolls Royce M250
At H.E.R.O.S. Inc., we take immense pride in being masters of the M250 engine. Our expertise and proficiency in this specific engine stem from years of dedicated focus, technical knowledge, and hands-on experience.
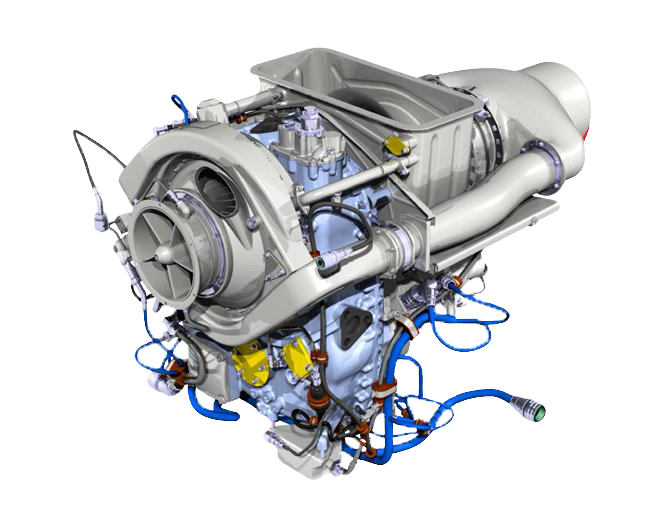
Our team members have accumulated extensive experience working with the M250 engine throughout their careers. This firsthand experience allows us to understand the engine’s intricacies, behavior, and maintenance requirements at a profound level. We have encountered and resolved a wide range of technical challenges, enabling us to provide comprehensive support and solutions to our customers.
Technical Knowledge
We possess in-depth technical knowledge of the M250 engine. We continually stay updated with the latest advancements, industry best practices, and maintenance procedures. This expertise ensures that we can accurately diagnose issues, perform effective maintenance, and provide valuable insights to optimize engine performance.
Ongoing Training
Ongoing training is essential to enhance our skills and stay at the forefront of the M250 engine industry. Our team members undergo rigorous training programs. These training programs validate our competence and ensure that we adhere to the highest standards of quality and safety.
Exceptional Customer Service
We place utmost importance on delivering exceptional customer service. Our team is dedicated to understanding the unique needs of our customers and providing tailored solutions that meet and exceed their expectations. We strive to build long-term relationships based on trust, reliability, and customer satisfaction.
Continuous Improvement
Our commitment to continuous improvement drives us to constantly seek ways to enhance our processes, optimize engine performance, and develop innovative solutions. We leverage tools such as Six Sigma and Lean Manufacturing to streamline our operations, minimize downtime, and maximize efficiency.
State of the Art Facilities
We invest in state-of-the-art facilities and advanced equipment to support our M250 engine expertise. These resources enable us to carry out comprehensive inspections, repairs, overhaul and testing with precision and accuracy.
Mastery of M250 Engine
Our mastery of the M250 engine is a result of our experience, technical knowledge, training, collaborative partnerships, customer-centric approach, commitment to continuous improvement, and top-notch facilities. With these factors in place, we are well-equipped to provide superior services and support to our customers, solidifying our reputation as masters of the M250 engine.
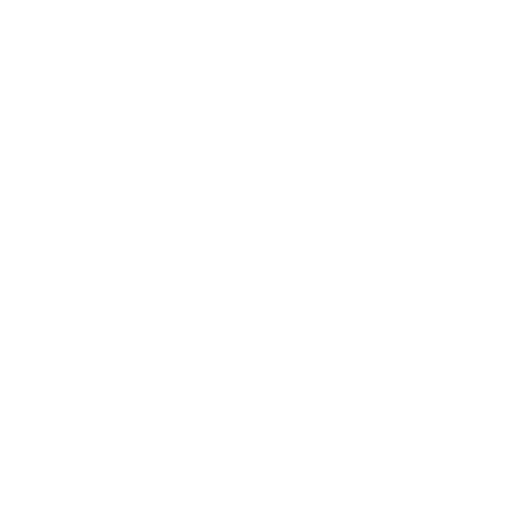
Engine Shop
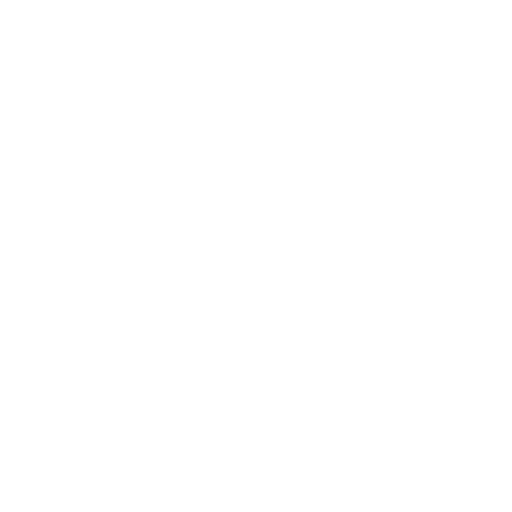
Machine Shop
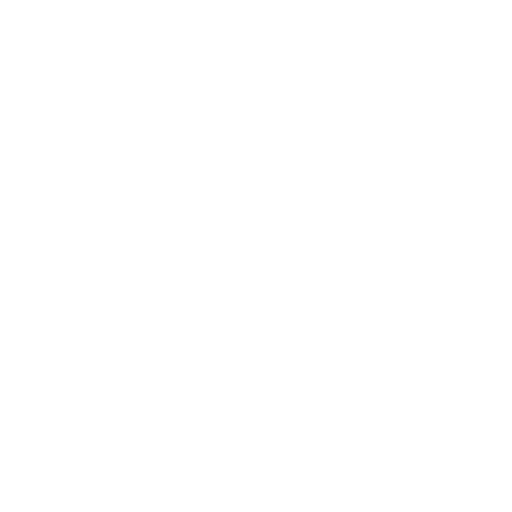
Accessory Shop
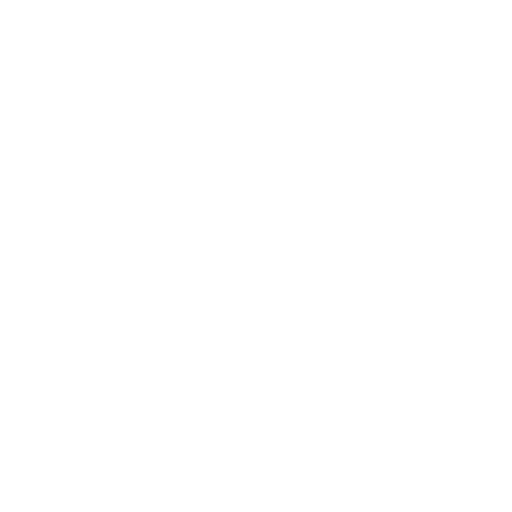
Accessory Testing
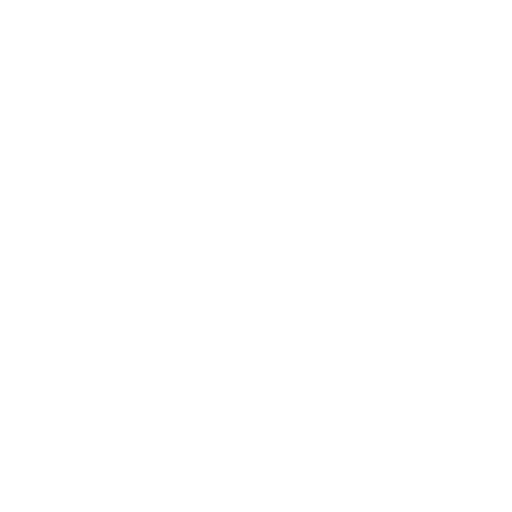
Test Cell
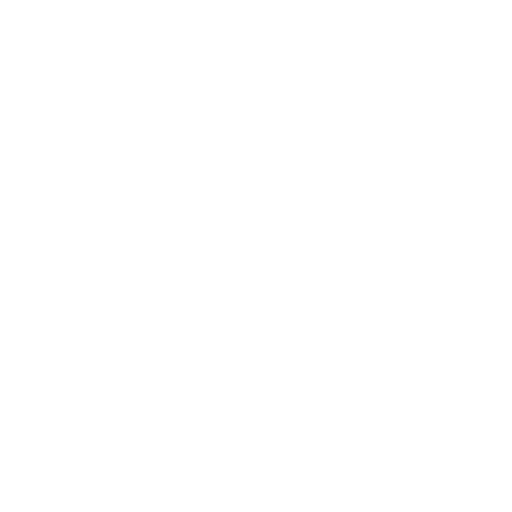
Non Destructive Testing
Engine Models
expand to see details
Series II TurboProp
M250-B17
- Cessna (American Jet Industries) 402 / 414
- Boeing (ASTA/GAF) Nomad N22
M250-B17B
- Cessna (American Jet Industries) 402 / 414
- Boeing (ASTA/GAF) Nomad N22
- Agusta (SiaiMarchetti) SM1019
- GIPPS Air
M250-B17C
- Cessna (American Jet Industries) 402 / 414
- Boeing (ASTA/GAF) N22 / N24 Nomad
- Beech (TradewindTurbines) A36
- Vulcanair (Partenavia) Spartacus
- Vulcanair (Partenavia) P68TP
- B‑NGroup BN‑2T
- Maule M‑7‑420
- FFA AS‑ 202 / 32TPBravo
- Enaer T‑35 Pillan
- GIPPS Air
M250B17F
- Aermacchi (Valmet) L90TP
- Beech (Allison) AT‑34
- Extra Aircraft EA‑500
- Grob G120TP
Series II Turboshaft
M250-C20
- AgustaWestland A109 / A109A
- Bell 206BJetRanger
- MDHI (Hughes) MD 500C
- Eurocopter BO 105C
M250-C20B
- Agusta Westland A109A / A109A MkII
- Bell206B‑3JetRanger III
- Bell 206L LongRanger I
- Bell TH‑ 57B SeaRanger
- Bell (Soloy)47/47G
- Eurocopter BO 105CBS
- Hiller (Soloy) UH‑12
- MDHI MD500D / 500E
- PZL Kania
- RFB Fantrainer 400
- Rogerson ‑ Hiller RH1100
M250-C20F
- Eurocopter AS355E / 355F TwinStar / TwinSquirrel
250-C20J
- Bell 206B‑3 JetRanger III
- Bell 206L TH‑57B/CSeaRanger
- TH‑67 Creek
250‑C20R
- Eurocopter AS355E /355F TwinStar / Twin Squirrel
- Bell 206LT TwinRanger
- Bell (Tridair) 206LGemini ST
250‑C20R/1
- AgustaWestland A109A
- MkII+ / A109C / A109C Max
Series IV Turboshaft
250‑C30
- Cessna (Soloy) 337Skymaster
- MDHI MD530F
- Sikorsky S‑76A
- RFB FanTrainer 600
250‑C30P
- Bell 206L‑3 LongRanger III
- Bell 206L‑4 LongRanger IV Calstar BO‑105LSSTC
250‑C40B – Bell430
250‑C47B – Bell 407 & Bell 407GX
250‑C47 B/8 – Bell GXP
250‑C47M – MDHI MD600N
Service
Engine Shop
Our Engine Shop offers a comprehensive range of services that cater to the maintenance, repair, and overhaul of M250 engines. From routine maintenance to intricate repairs, we meticulously inspect, diagnose and identifying any issues or potential problems.
With a deep understanding of M250 engines and 135 years of combined experience, we provide tailored solutions to optimize engine performance and extended lifespan.
We offer an extensive range of material choices from:
- New Factory
- Airworthy
- PMA (Parts Manufacturer Approval)
Products
As an independent FAA and EASA authorized MRO facility, we offer a wide array of M250 model overhaul and repairs, which include the following rated engine series:
- M250-B17
- M250-C18
- M250-C20
- M250‑C30 (Excludes M250‑C30R/3D)
- T63-A-720
- M250-C40B
- M250-C47B
- M250-C47B/8
- M250-C47/M
Tools
Our state-of-the-art test cell provides both functional and performance testing for M250 series gas turbine engines.
H.E.R.O.S. Inc. is committed to delivering reliable engines that perform and remain on wing.
Engine testing capabilities include:
- Performance Testing
- Diagnostics / Analysis
- Troubleshooting
- Third Party Testing
Service
Machine Shop
We consider our machine shop a center of excellence, bringing an exceptional experience to all of our customers. We bring this functional expertise to every product we machine.
Our machine shop can work with a variety of components commonly used in the M250 aerospace field. By leveraging our expert skills, we strive to achieve exacting accuracy and functionality, our CNC machines reduce the risk of human error while restoring and precision machining of components.
Machining Services
- Gearbox Housing & Covers
- PT Supports Seals
- Diffuser Assembles
- Nozzles Blade Tip Paths
- Oil Sump Covers
- Bleed Valves
- Oil Filter Housings
- Scrolls
- Combustors
- Fuel Pump Bypass
- Valve Seat
- PT Govenor Covers & Bushings
Tools
The optimal choice for your machining needs is very dependent on the shape and machined features. We have found that using a variety of equipment makes us much more versatile and efficient.
- (1) CNC 2.5 axis mill
- (3) CNC 3 axis mills
- (1) Horizontal Lathe
- (2) Moore Jig Grinders
- Mitutoyo CMM
Service
Accessory Shop
Our accessory shop provides a full range of repair and overhaul capabilities, ensuring every accessory component receives the same exceptional quality and expertise as their engines, propelling your aircraft to new heights of performance and reliability.
We provide our customers with readily available components of the highest quality at the best price. Our trained and experienced technicians offer solutions focused on the most economical means of maintaining your components. With our flat-Rate Overhaul and Exchange options, we ensure cost-effective solutions for eligible core part numbers.
Additionally, we offer an extensive range of part choices, including New Factory, Airworthy options and PMA (Parts Manufacturer Approval) certified components, giving you a wide selection to meet your specific needs.
Offering industry-leading aviation MRO services:
- Exceptional On-Wing Performance
- Unsurpassed Turn-Time
- Outstanding Customer Service
- Wide selection of recertified exchange
Products
Eaton
Fuel Pumps Models
- 386500-4
- 386500-5
- 388100-5
- 394400 Series
HAMILTON STANDARD / HAMILTON SUNSTRAND / GOODYEAR / UTC AEROSPACE
Fuel Pumps Models
- 5004506
- 024918-107
- 5002395C
- 5002395D
HONEYWELL
Check Valves
- 252449-3 / 6873599
- 2554502-1 / 6876557
Fuel Control Models
- DP-D3
- DP-M1
- DP-P2
Power Turbine Governor Models
- AL-AA1
- AL-AA2
- AL-AC1
- AL-AC3
- AL-AD1
- AL-AD2
- AL-L3
- AL-L4
HONEYWELL / ALLIED SIGNAL / BENDIX
Governor and Gas Turbine Fuel Control Models
- DP-N2
- DP-T3
- DP-V1
Tools
Available test benches:
- Oil Pump & Oil Jet
- Fuel Pump & Check Valve
- Power Turbine Governor
- Bleed Valve / Pc Air Filter / Anti-Icing Valve
- Fuel Control Orifices Pre-Set
- Fuel Nozzle Assemble
- Fuel Control Calibration
Service
Accessory Testing
H.E.R.O.S. Inc. offers a wide variety of in-shop maintenance, repairs, overhauls and troubleshooting of M250 accessories. We utilize several test benches to ensure our customers receive a quality component.
All accessories are fully bench tested to ensure test limits are met as well as meeting our own quality standards.
Products
At H.E.R.O.S. Inc. our accessory shop has the capability and specializes in the overhaul and repair of the following M250 Accessories.
We also perform Overhaul, Test and Repair on our Rated Engines Compressor Bleed Valves, Anti-Ice Valves & Fuel Nozzles.
Eaton
Fuel Pumps Models
- 386500-4
- 386500-5
- 388100-5
- 394400 Series
HAMILTON STANDARD / HAMILTON SUNSTRAND / GOODYEAR / UTC AEROSPACE
Fuel Pumps Models
- 5004506
- 024918-107
- 5002395C
- 5002395D
HONEYWELL
Check Valves
- 252449-3 / 6873599
- 2554502-1 / 6876557
Fuel Control Models
- DP-D3
- DP-M1
- DP-P2
Power Turbine Governor Models
- AL-AA1
- AL-AA2
- AL-AC1
- AL-AC3
- AL-AD1
- AL-AD2
- AL-L3
- AL-L4
HONEYWELL / ALLIED SIGNAL / BENDIX
Governor and Gas Turbine Fuel Control Models
- DP-N2
- DP-T3
- DP-V1
Tools
Available test benches:
- Oil Pump & Oil Jet
- Fuel Pump & Check Valve
- Power Turbine Governor
- Bleed Valve / Pc Air Filter / Anti-Icing Valve
- Fuel Control Orifices Pre-Set
- Fuel Nozzle Assemble
- Fuel Control Calibration
Service
Test Cell
Our state-of-the-art test cell provides both functional and performance testing for M250 series gas turbine engines. H.E.R.O.S. Inc. is committed to delivering reliable engines that perform and remain on wing.
Our test cell provides a dynamic touch to ensure a quality product our customers can rely on. The test cell itself is easily configurable to fit any of our M250 engines (turboprop or turboshaft).
Testing Capabilities
- Performance Testing
- Diagnostics / Analysis
- Troubleshooting
- Third Party Testing
Models Tested
- M250-B17B/C/F Series II Turboprop
- M250-C18 Series I Turboshaft
- M250-C20B/F/J/R/W Series II Turboshaft
- T63-A-720 Series I Turboshaft
- M250-C30 /G/M/S/P/HU Series IV (excludes M250-C30R/3D) Turboshaft
- M250-C40, C47B/M Series IV Turboshaft
Service
Non-Destructive Testing (NDT)
At H.E.R.O.S., we offer two types of Non-Destructive Testing (NDT), including both Magnetic Particle Inspection (MPI) and Fluorescent Penetrant Inspection (FPI).
Magnetic Particle Inspection (MPI)
Magnetic Particle Inspection (MPI) is a non-destructive testing method used to detect surface and near-surface defects in ferromagnetic materials. It relies on the principles of magnetism.
In MPI, a magnetic field is applied to the test material, and ferrous particles (usually iron or iron oxide) are applied to the surface. When defects or cracks disrupt the magnetic field, the particles cluster at these locations, creating visible indications that can be easily examined.
MPI Capabilities
Surface and Near-Surface Flaw Detection: MPI is particularly effective for detecting surface and near-surface defects in ferromagnetic materials, including cracks, inclusions, laps, seams, and other anomalies.
Rapid Inspection: MPI is a relatively quick testing method, making it suitable for applications where speed is important, such as production environments.
Real-Time Inspection: Results can be observed in real time, allowing for immediate decision-making and immediate re-inspection if necessary.
Cost-Effective: MPI is considered cost-effective for many applications, especially when compared to other NDT methods.
MPI Tools
Magnetic Particles: Iron or iron oxide particles, either dry or suspended in a liquid, are applied to the surface of the test piece. These particles accumulate at defect locations under the influence of the magnetic field.
Fluorescent Particle Inspection Materials: These materials are used to make the particles visible. In some cases, they are applied as a contrasting background to improve the visibility of indications.
UV Light Source: For fluorescent MPI, a UV light source is used to excite the fluorescent particles, making the indications visible.
Wet Particle Application Equipment: Wet particles are used, application equipment used are suspension tanks.
Cleaners and Removers: These are used to clean the surface after testing to remove excess particles.
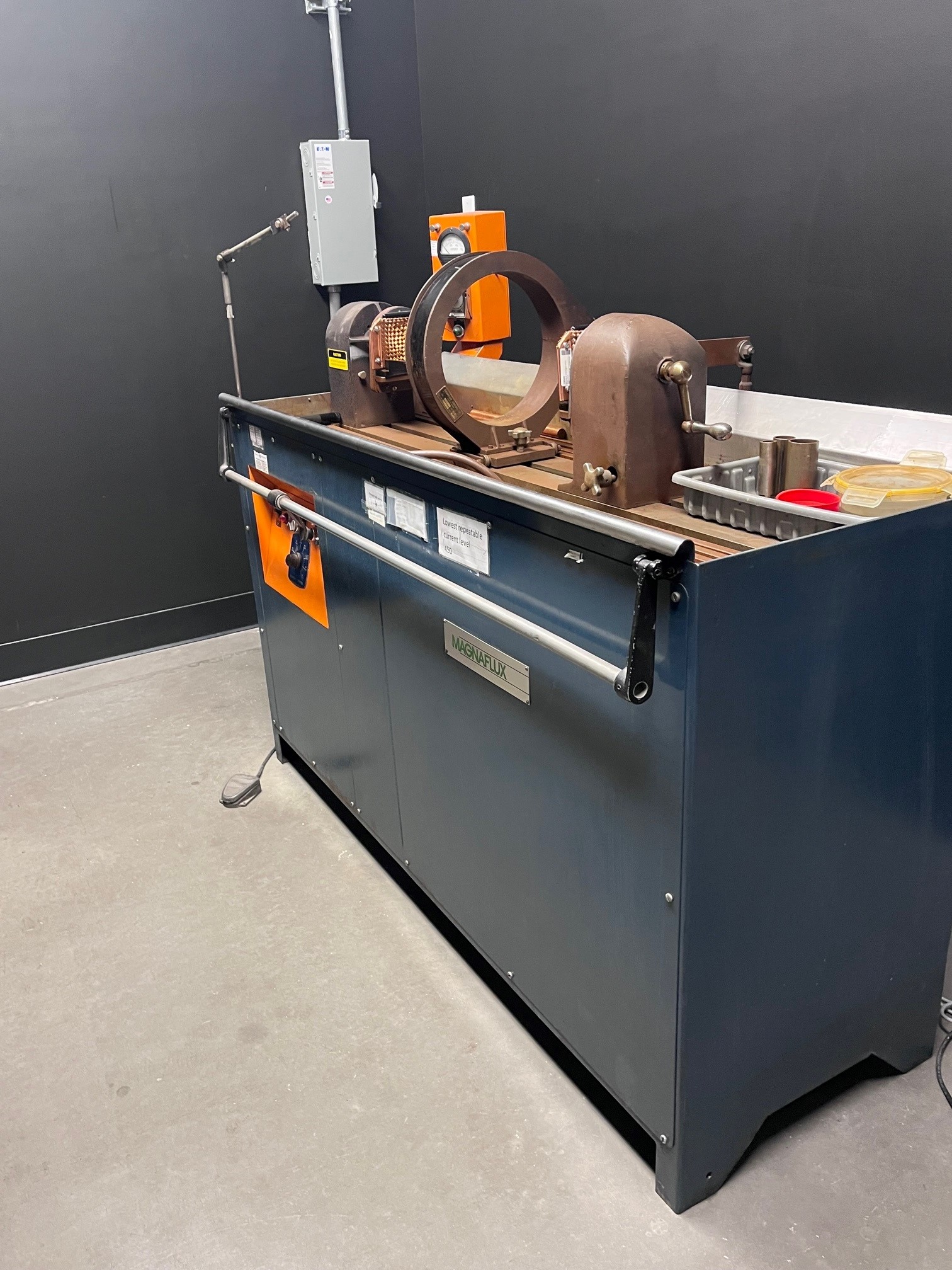
Fluorescent Penetrant Inspection (FPI)
Fluorescent Penetrant Inspection (FPI), is a fluorescent dye applied to the surface of a non-porous material in order to detect defects that may compromise the integrity or quality of the part in question. It is a non-destructive testing (NDT) method used to detect surface-breaking defects or discontinuities in various materials, including metals, plastics, ceramics, and composites.
This method FPI involves the application of a colored or fluorescent liquid penetrant to the test surface, which is then drawn into any surface defects through capillary action. Afterward, excess penetrant is removed, and a developer is applied to make the indications visible for examination.
FPI Capabilities
Surface Defect Detection: Is highly effective at identifying surface-breaking defects, including cracks, seams, laps, porosity, and other discontinuities.
Sensitivity: Can detect very small defects, often on the order of a few thousandths of an inch, making it suitable for high-precision applications.
Materials: Can be used on a wide range of materials, including metals, ceramics, plastics, and composites, as long as they are not highly porous.
Color Contrast and Fluorescence: Offers color contrast and fluorescent options, making it possible to detect indications under different lighting conditions.
Versatility: Can be applied to complex shapes and intricate geometries, and it can be used for both laboratory and field inspections.
Liquid Penetrant Inspection (FPI) Tools:
Penetrant Materials: These include the liquid penetrant itself, which can be either colored or fluorescent, as well as developer materials for making indications visible.
Penetrant Application Equipment: Dip tanks are used to apply the penetrant to the surface of the test piece.
Developer Application Equipment: Similar to penetrant application, developer materials are applied to the surface to draw out penetrant from defects and make them visible. This is done developer powders.
Cleaners and Removers: These are used to clean the surface of the test piece before applying the penetrant and to remove excess penetrant after the dwell time.
UV Light Source (for fluorescent penetrants): In fluorescent penetrant inspection (FPI), a UV light source is used to excite the fluorescent penetrant, making indications visible.
Safety Equipment: When working with UV fluorescent penetrants, technicians may use protective goggles and clothing to shield themselves from UV radiation.
Visual Inspection Equipment: This includes the use of adequate lighting, magnifying glasses, and other tools to inspect the test piece for indications.
Cleaning Materials: Solvents, cleaning brushes, and rags are used to ensure the test piece’s surface is clean before the application of penetrant.
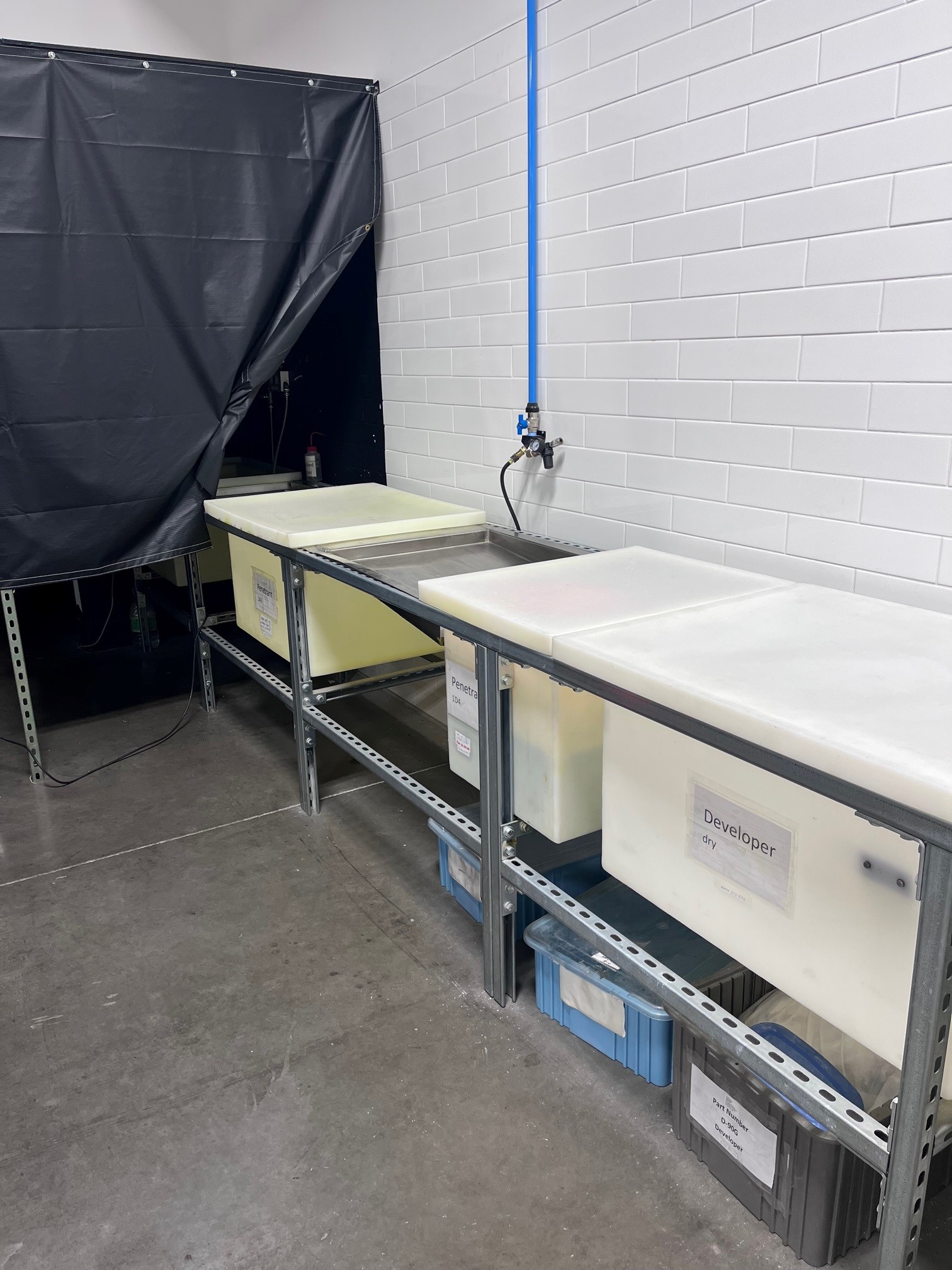